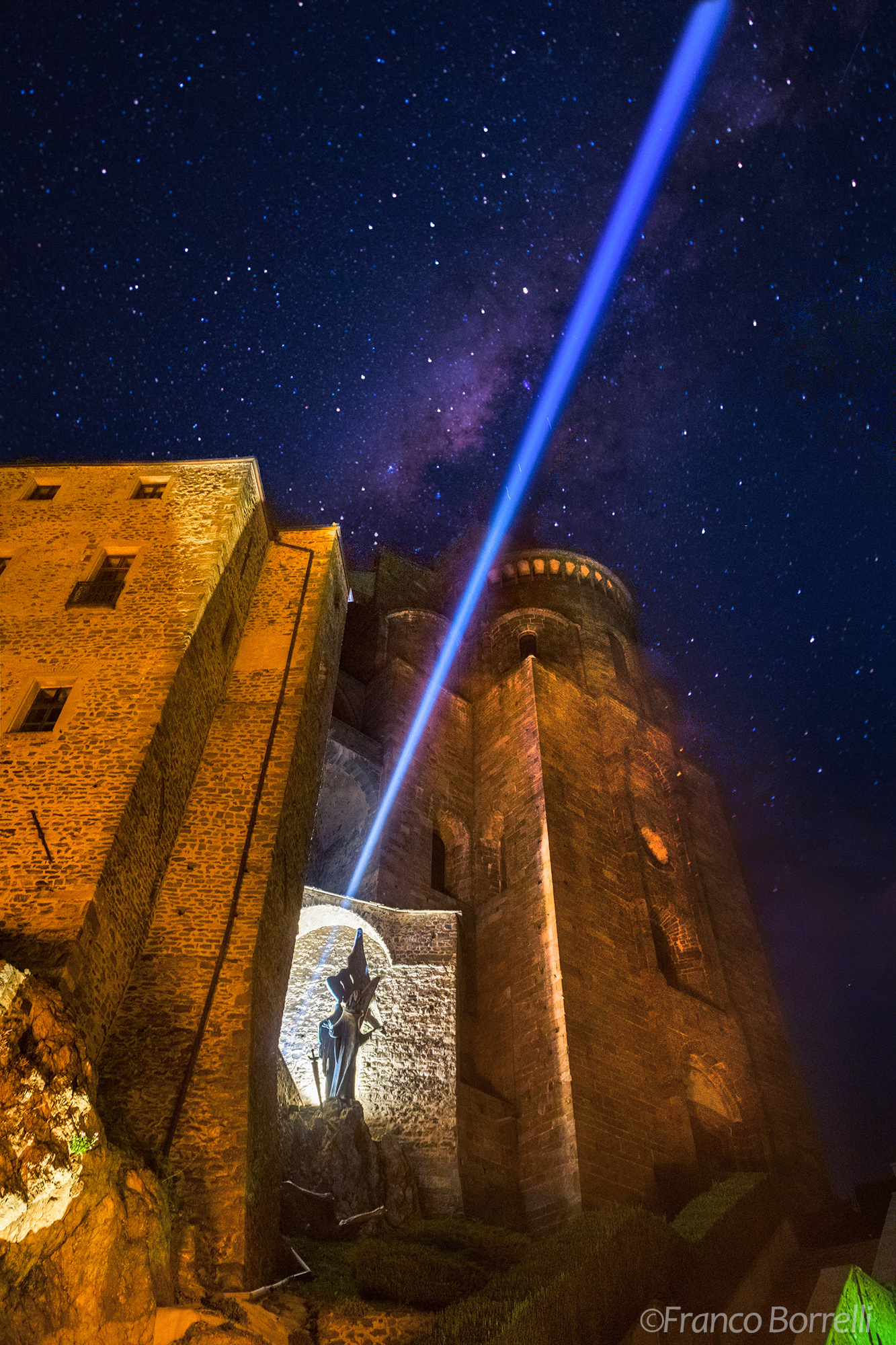
La Spada di Luce
“La Spada di Luce ” si รจ innalzata nel cielo, partendo dalla Sacra di San Michele, la prima volta nel 2021 e poi nel 2023. Un raggio di luce di 7 km che ha unito cielo e terra.
Gallery
See it in action1000 anni di storia illuminati nella notte
Una installazione visiva che rievoca un antico sapere
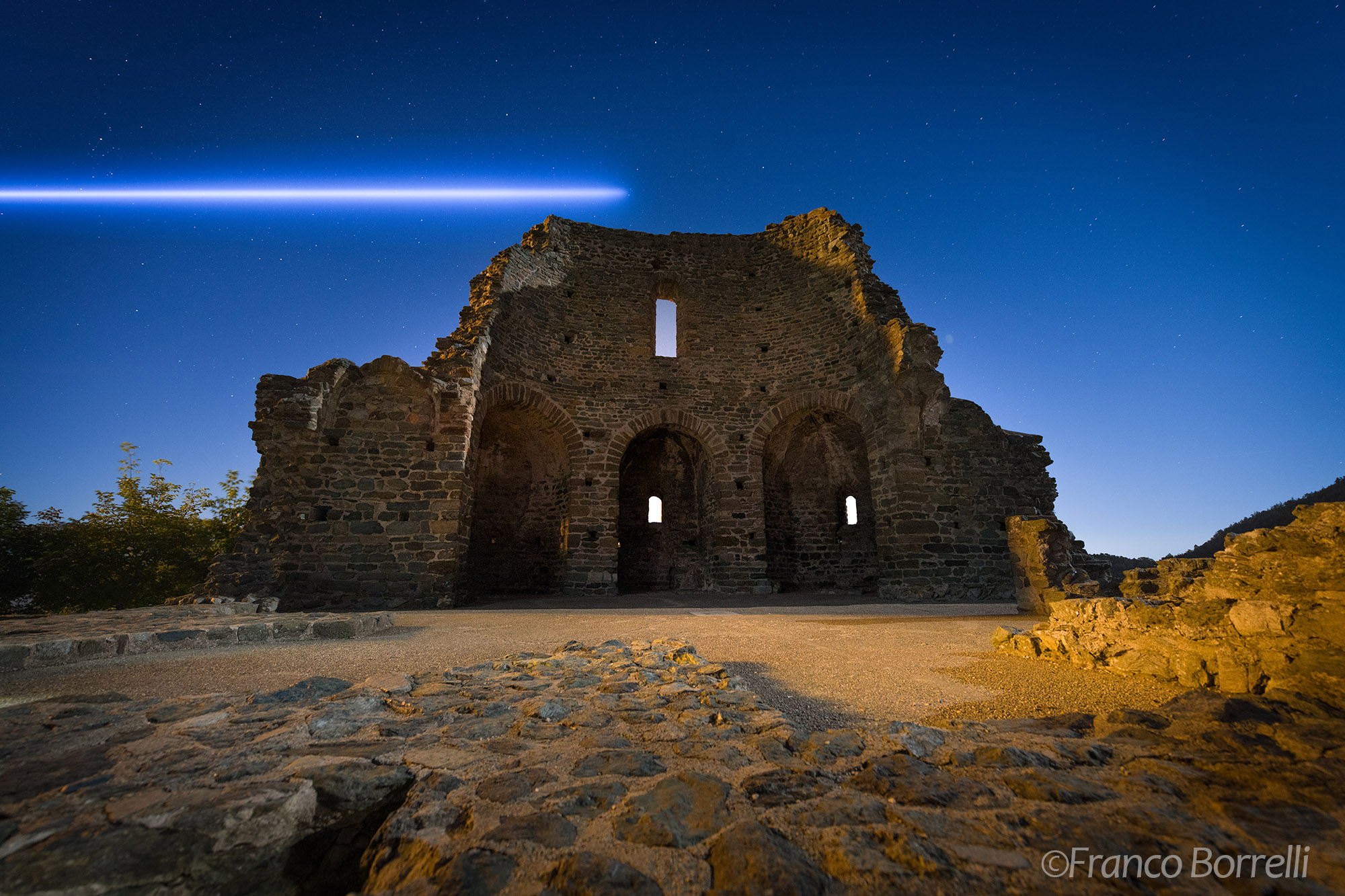
Contact us
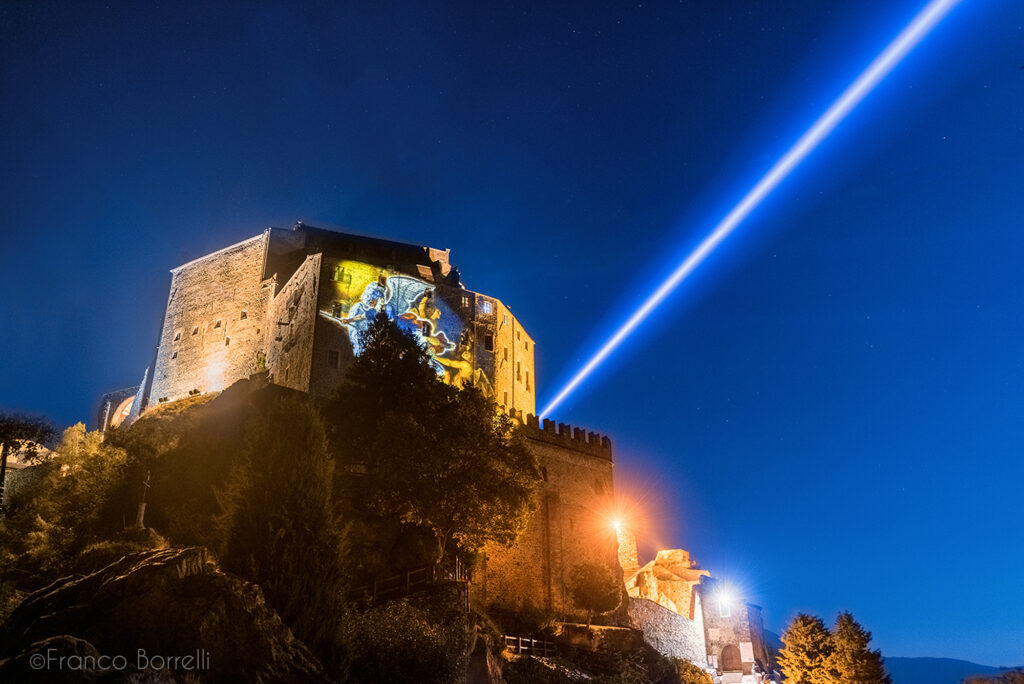
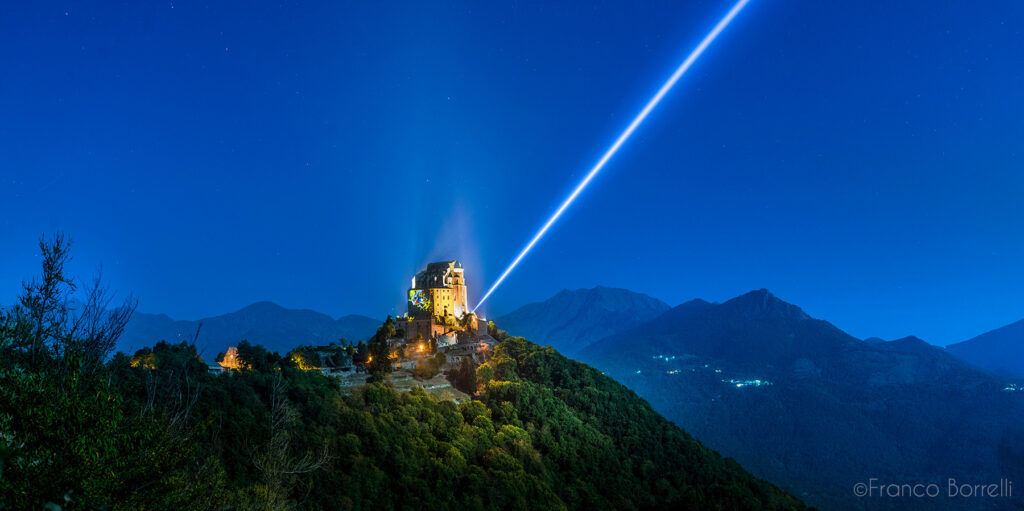
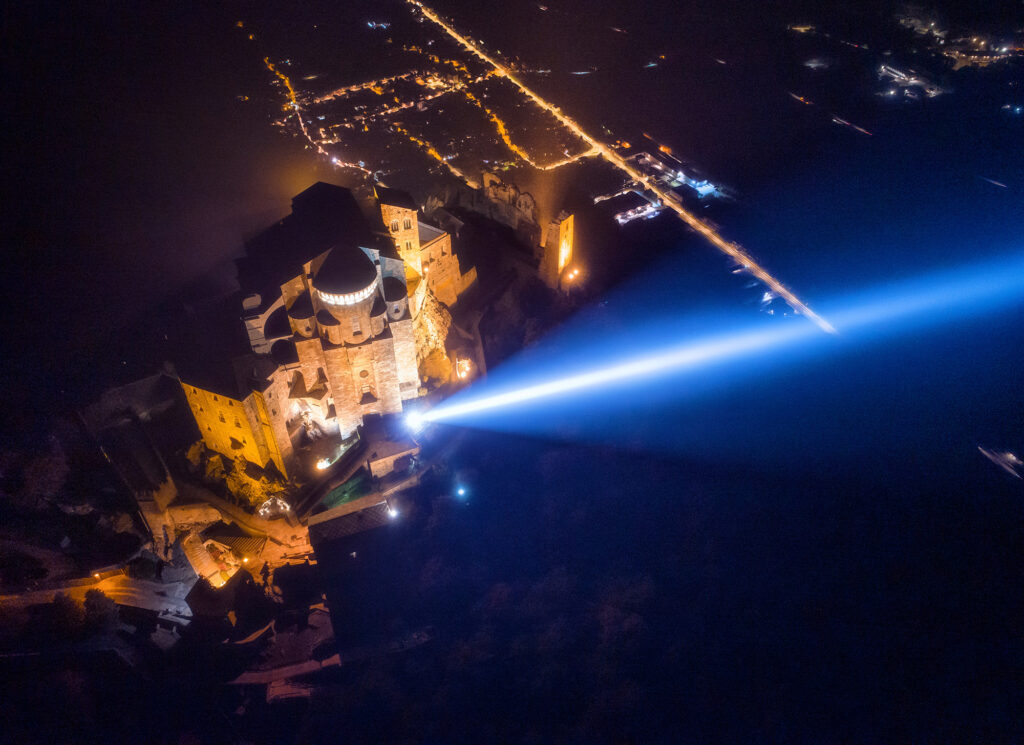